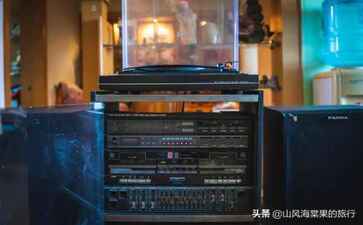
頭屯河區(qū)令首保溫容器股份有限公司位于頭屯河區(qū),頭屯河區(qū)令首保溫容器股份有限公司m.020zhuce.cn經(jīng)營(yíng)范圍含:焊接設(shè)備、水利水電、培訓(xùn)、皮革加工、工業(yè)機(jī)械、運(yùn)動(dòng)健康、水果、行政、普拉提、工程監(jiān)理(依法須經(jīng)批準(zhǔn)的項(xiàng)目,經(jīng)相關(guān)部門批準(zhǔn)后方可開(kāi)展經(jīng)營(yíng)活動(dòng))。。
頭屯河區(qū)令首保溫容器股份有限公司為了深入貫徹黨中央和國(guó)務(wù)院對(duì)國(guó)有企業(yè)深化改革的重要部署,并嚴(yán)格按照國(guó)資委關(guān)于推動(dòng)企業(yè)做大做強(qiáng)的指示精神,我們將堅(jiān)定不移地推動(dòng)企業(yè)改革進(jìn)程,持續(xù)優(yōu)化調(diào)整產(chǎn)業(yè)結(jié)構(gòu),實(shí)現(xiàn)資源的科學(xué)配置,從而增強(qiáng)企業(yè)的核心競(jìng)爭(zhēng)力。同時(shí),我們將全面提升企業(yè)素質(zhì),積極面向國(guó)際和國(guó)內(nèi)兩個(gè)市場(chǎng),以更加堅(jiān)定的步伐和更加遠(yuǎn)大的目標(biāo),努力奮進(jìn),為企業(yè)的持續(xù)健康發(fā)展奠定堅(jiān)實(shí)基礎(chǔ)。
頭屯河區(qū)令首保溫容器股份有限公司在發(fā)展中注重與業(yè)界人士合作交流,強(qiáng)強(qiáng)聯(lián)手,共同發(fā)展壯大。在客戶層面中力求廣泛 建立穩(wěn)定的客戶基礎(chǔ),業(yè)務(wù)范圍涵蓋了建筑業(yè)、設(shè)計(jì)業(yè)、工業(yè)、制造業(yè)、文化業(yè)、外商獨(dú)資 企業(yè)等領(lǐng)域,針對(duì)較為復(fù)雜、繁瑣的行業(yè)資質(zhì)注冊(cè)申請(qǐng)咨詢有著豐富的實(shí)操經(jīng)驗(yàn),分別滿足 不同行業(yè),為各企業(yè)盡其所能,為之提供合理、多方面的專業(yè)服務(wù)。
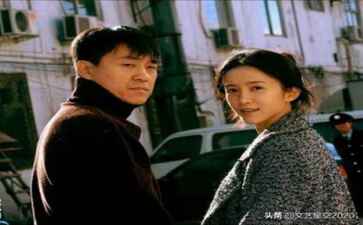
頭屯河區(qū)令首保溫容器股份有限公司秉承“質(zhì)量為本,服務(wù)社會(huì)”的原則,立足于高新技術(shù),科學(xué)管理,擁有現(xiàn)代化的生產(chǎn)、檢測(cè)及試驗(yàn)設(shè)備,已建立起完善的產(chǎn)品結(jié)構(gòu)體系,產(chǎn)品品種,結(jié)構(gòu)體系完善,性能質(zhì)量穩(wěn)定。
頭屯河區(qū)令首保溫容器股份有限公司是一家具有完整生態(tài)鏈的企業(yè),它為客戶提供綜合的、專業(yè)現(xiàn)代化裝修解決方案。為消費(fèi)者提供較優(yōu)質(zhì)的產(chǎn)品、較貼切的服務(wù)、較具競(jìng)爭(zhēng)力的營(yíng)銷模式。
核心價(jià)值:尊重、誠(chéng)信、推崇、感恩、合作
經(jīng)營(yíng)理念:客戶、誠(chéng)信、專業(yè)、團(tuán)隊(duì)、成功
服務(wù)理念:真誠(chéng)、專業(yè)、精準(zhǔn)、周全、可靠
企業(yè)愿景:成為較受信任的創(chuàng)新性企業(yè)服務(wù)開(kāi)放平臺(tái)
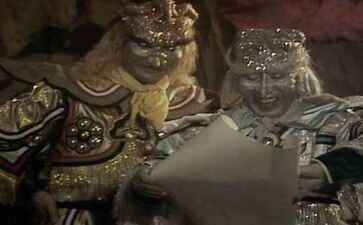